Basic Info.
Model NO.
Steel Exhaust Pipe
Application
Auto Parts
Machining
Machining Center
Material
Steel
Surface Treatment
Sand Blast
Surface Roughness
Ra12.5
Standard
ASTM
Certification
ISO 9001:2008, TF16949
Transport Package
Bubble Bag, Carton, Pallets or Wooden Box
Specification
Drawing
Trademark
OEM
Origin
China
HS Code
73269090
Production Capacity
8000 Tons Per Year
Product Description
Brief introduciton of sand casting:
Sand casting is perhaps the oldest and most commonly used type of metal forming in the marketplace today. It is capable of forming both large and small parts and can be used for a number of different materials.
We have green sand castings, resin sand casings and water glass sand castings in both ferrous and non-ferrous materials.
Perhaps the most common green sand castings would be made from either grey iron or ductile iron. We can supply these castings from approximately 0.05Kg to approximately 15000 Kg and up to 5000mm x 2000mm x 1500mm in size for the largest part. Molding methods range from floor hand molding, jolt squeezer lines and automatic molding lines. With this variety of molding methods we are able to accommodate the weight, size and quantity the customer requires.
Steel sand castings are available both as water glass sand castings and resin sand castings, and are available in plain carbon, alloy and stainless steels. In the category of steel sand castings the smallest available part would be approximately 1Kg while the largest would be approximately 20 tons. Steel castings smaller than the 1Kg range would be made from investment casting(lost wax casting) method.
Non-ferrous sand castings are also available. The molding process used is green sand and we can accommodate requests for castings weighing from 0.1 Kg to 100 Kg. The alloys that are available include copper base and aluminum base alloys.
First article layouts and spectrometer material certifications are provided with all first article samples. Specialized inspection reports can be done per customer request.
A variety of secondary operations can be performed on all three types of sand castings. They include shot blasting, heat treatment, machining,surface treatment, assembly services and even custom packaging.
Chemical composition of some materials:
Some sand casting process:
Machining and inspection equipments:
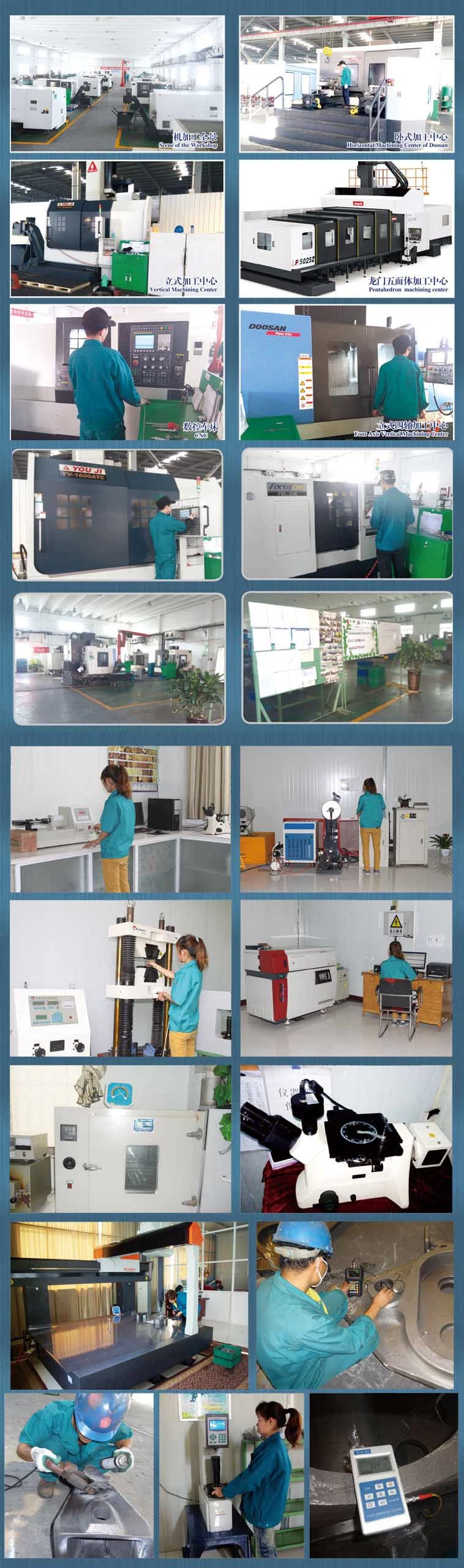
Some products:
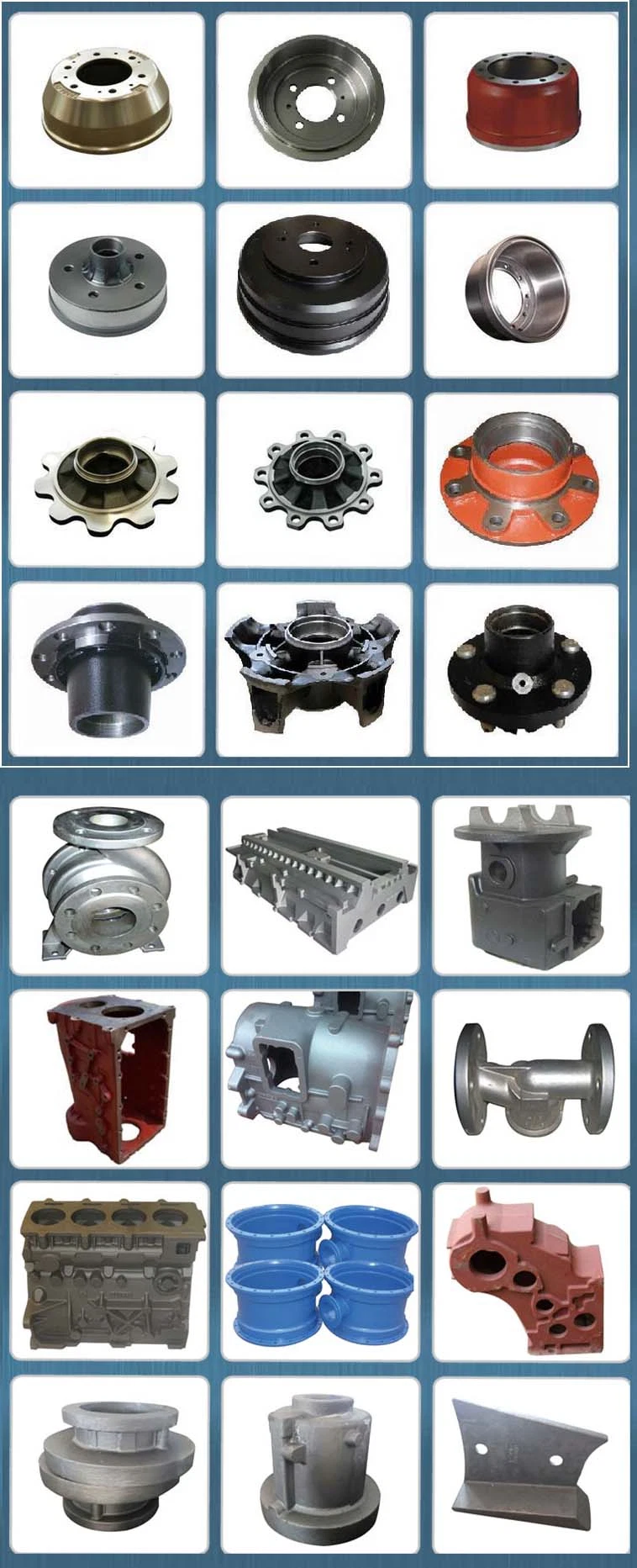
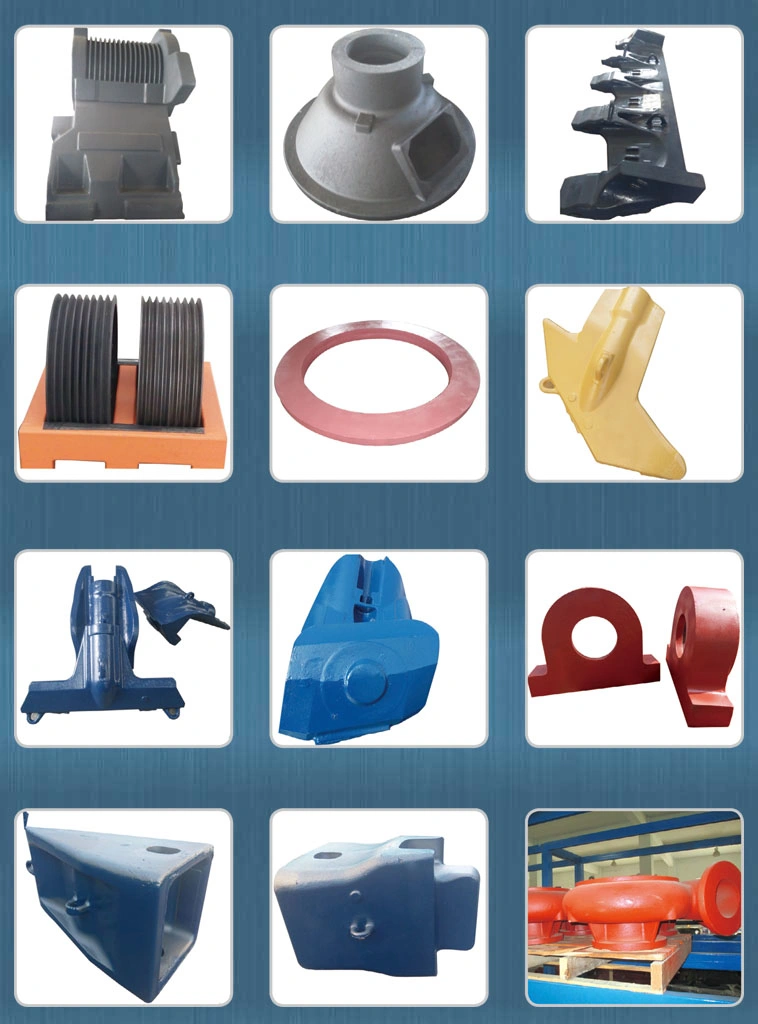
Packing and customers:
Our advantages:
1. 20 years of manufacturing success in China and exporting experience worldwide
2.Global specialized producer of machined castings.
3. We combine our own resources with some other well-developed factories to fulfill a wide range of contract manufacturing capabilities. Working with one source, saves time and money.
4. Satisfied supplier of 7 big companies from North America and Europe.
5. Low cost mold materials and focus on efficiency offer a cost-effective solution to your metal component purchasing requirements.
6. Normal lead times range from 1 to 6 weeks for fully-machined components.
7. Strong capacity to help customers develop new projects.
8. Our sales department is 24 hours available in order to help our customers solve problems quickly.
Contact Donrex today and begin enjoying the benefits of high quality and low price products.
Sand casting is perhaps the oldest and most commonly used type of metal forming in the marketplace today. It is capable of forming both large and small parts and can be used for a number of different materials.
We have green sand castings, resin sand casings and water glass sand castings in both ferrous and non-ferrous materials.
Perhaps the most common green sand castings would be made from either grey iron or ductile iron. We can supply these castings from approximately 0.05Kg to approximately 15000 Kg and up to 5000mm x 2000mm x 1500mm in size for the largest part. Molding methods range from floor hand molding, jolt squeezer lines and automatic molding lines. With this variety of molding methods we are able to accommodate the weight, size and quantity the customer requires.
Steel sand castings are available both as water glass sand castings and resin sand castings, and are available in plain carbon, alloy and stainless steels. In the category of steel sand castings the smallest available part would be approximately 1Kg while the largest would be approximately 20 tons. Steel castings smaller than the 1Kg range would be made from investment casting(lost wax casting) method.
Non-ferrous sand castings are also available. The molding process used is green sand and we can accommodate requests for castings weighing from 0.1 Kg to 100 Kg. The alloys that are available include copper base and aluminum base alloys.
First article layouts and spectrometer material certifications are provided with all first article samples. Specialized inspection reports can be done per customer request.
A variety of secondary operations can be performed on all three types of sand castings. They include shot blasting, heat treatment, machining,surface treatment, assembly services and even custom packaging.
Materials and casting weights for different sand casting methods | |||
Sand casting method | Green sand casting | Resin sand casing | Water glass sand casting |
Materials used in different method | Grey iron,Ductile iron, Aluminum and copper alloy | Grey iron,Ductile iron, Carbon steel,Alloy steel, Stainless steel | Carbon steel,Alloy steel, Stainless steel |
Weight range | 0.05-15000Kg | 0.5-18000Kg | 5-20000Kg |
Chemical composition of some materials:

Some sand casting process:

Machining and inspection equipments:
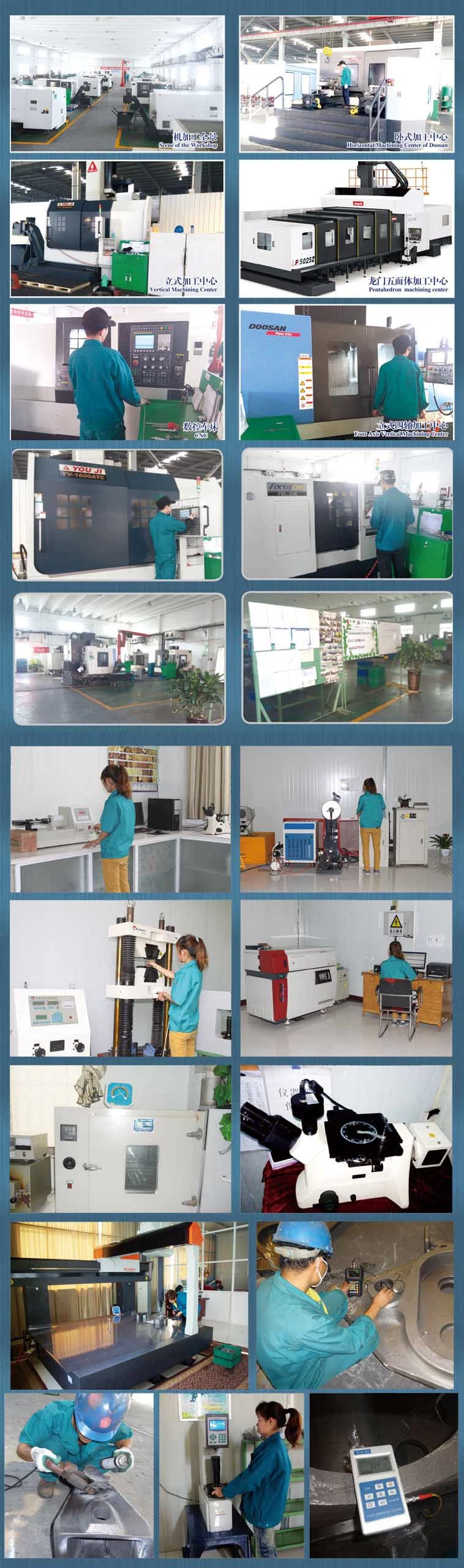
Some products:
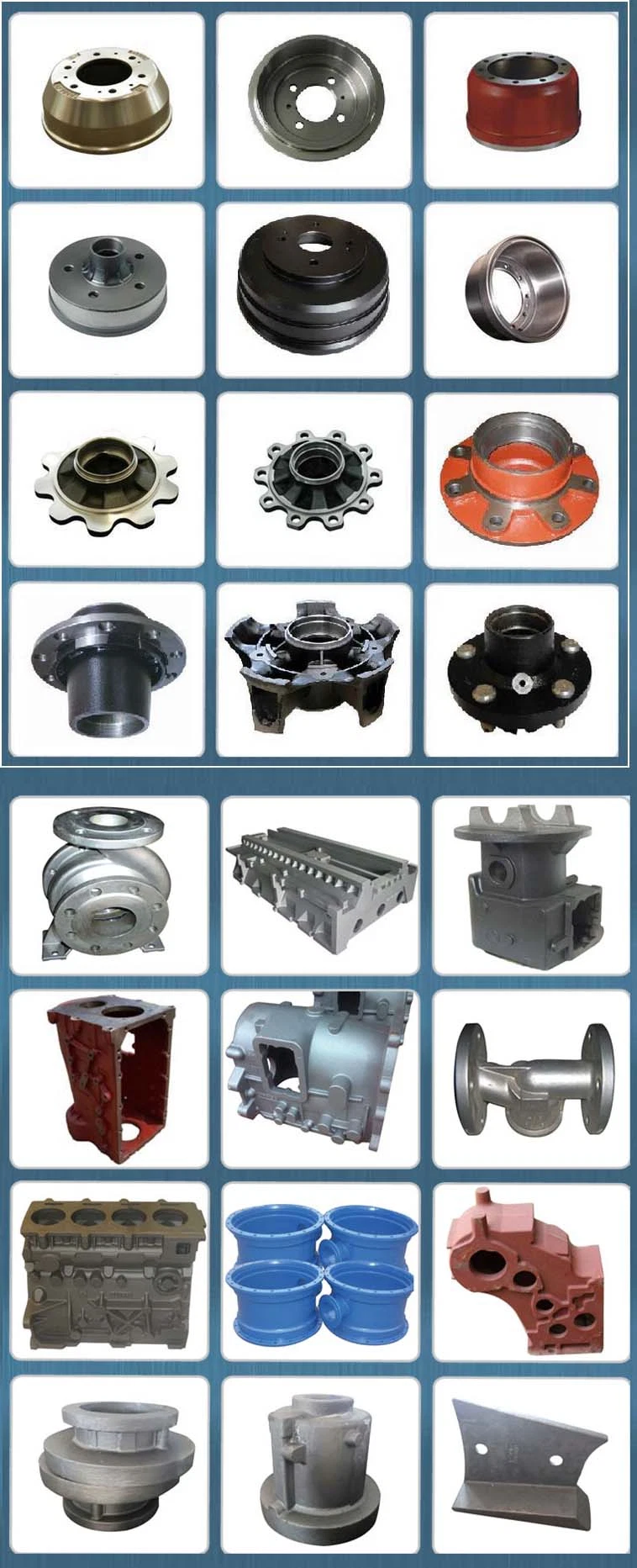
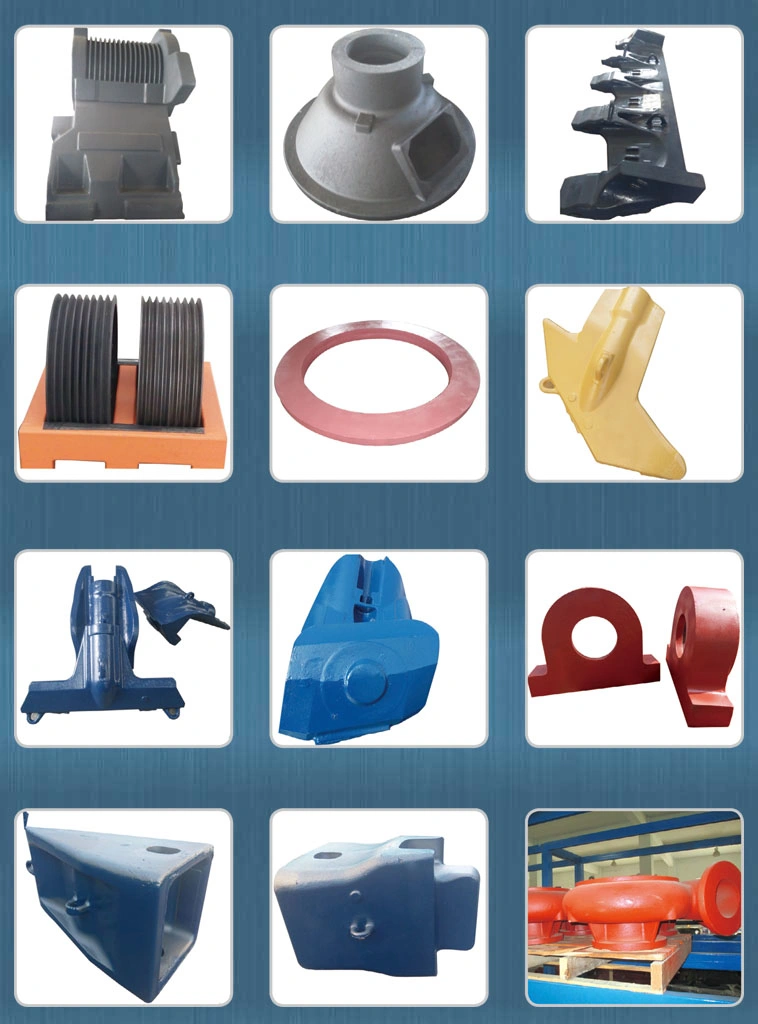
Packing and customers:

Our advantages:
1. 20 years of manufacturing success in China and exporting experience worldwide
2.Global specialized producer of machined castings.
3. We combine our own resources with some other well-developed factories to fulfill a wide range of contract manufacturing capabilities. Working with one source, saves time and money.
4. Satisfied supplier of 7 big companies from North America and Europe.
5. Low cost mold materials and focus on efficiency offer a cost-effective solution to your metal component purchasing requirements.
6. Normal lead times range from 1 to 6 weeks for fully-machined components.
7. Strong capacity to help customers develop new projects.
8. Our sales department is 24 hours available in order to help our customers solve problems quickly.
Contact Donrex today and begin enjoying the benefits of high quality and low price products.